Showing 6 results for Graphite
A. Ahmadi,, H. Sarpoolaky,, A. Mirhabibi, F. Golestani-Fard,
Volume 4, Issue 3 (12-2007)
Abstract
Abstract: Dolomite based refractories are widely used in Iranian steelmaking plants. In the
present research, wear and corrosion of refractories used in steel-making converter lining in
Esfahan Steel Company was studied. Post-mortem analysis of refractories clarified that the wear
started with oxidation of carbon followed by chemical corrosion. Iron oxide from slag reacted with
calcia, resulting in formation of low melting phase, and subsequent washout process, caused the
refractory corrosion onset from the hot face. In addition, the effect of aluminum as an anti-oxidant
and graphite on the corrosion resistance of refractory was investigated. Tar-dolomite samples
containing different amount of graphite (0, 4, 7, and 10 wt. %) were prepared in order to study
their physical properties, before and after coking. SEM micrographs employed to analyze the
microstructures to determine the effect of graphite and antioxidant on corrosion behavior of the
refractory. Results showed that oxidation process of carbon in the system was hindered and
improved corrosion resistance by introducing graphite and antioxidant into the refractory
composition.
S. Niksirat, Sh. Raygan, S. Moradi Ghiassabadi,
Volume 12, Issue 2 (6-2015)
Abstract
In this research, two different carbonaceous materials (Graphite:G and Petrocoke:P) were separately
compared in terms of the carbothermic reduction of hematite and anatase in order to synthesize Fe-TiC nanocrystalline composite by mechanically activated sintering method. Powders were activated in a planetary high-energy
ball mill under argon atmosphere for 0, 2, 5, 10,and 20 h. Then, the activated powders were analyzed by XRD and
SEM to investigate phase constituents and microstructure of the mixtures. Results proved that Fe
2
O
3
and TiO
2
were not
reduced by carbonaceous materials even after 20h of milling. SEM investigations showed that G-mixture was more
homogenous than P-mixture after 20h of milling, meaning that graphite-anatase-hematite was mixed satisfactorily.
Thermogravimetry analysis was done on 0 and 20h milled powders. TG and DTG curves showed that mechanical
activation led to almost 300°C decrease in the reduction temperature of hematite and anatase in both mixtures. In the
next step, the powders were sintered in a tube furnace under argon atmosphere. In the G-mixture, anatase was reduced
to titanium carbide at 1100°C but, in the P-mixture, temperature of 1200°C was essential for completely reducing
anatase to titanium carbide.Results of phase identification of the sintered powders showed that anano-crystalline ironbased composite with titanium carbide, as the reinforcement was successfully synthesized after 20 h high-energy
milling of the initial powders and subsequent sintering occurred at 1200˚C for 1h
R. Khoshhal, M. Soltanieh, M. A. Boutorabi,
Volume 13, Issue 1 (3-2016)
Abstract
Al2O3/TiC composites are used as cutting tools for machining gray cast iron and steels. The addition of iron improves the toughness of Al2O3/TiC composites. Ilmenite, aluminum and graphite can be used to produce in-situ Al2O3/TiC–Fe composites. However, the formation mechanism and reaction sequences of this system are not clear enough. Therefore, the present research is designed to determine the reactions mechanism of the first step of reactions that may be occurred between raw materials. In this research, pure ilmenite was synthesized to eliminate the effects of impurities available in the natural ilmenite in the system. The milled and pressed samples, prepared from the synthesized ilmenite, aluminum and graphite mixture with a molar ratio of 1:2:1, were heat treated at 720°C for 48h. In addition, two samples one containing ilmenite and aluminum with a molar ratio of 1:2 and ilmenite and graphite with a molar ratio of 1:1 were heat treated at 720°C for 48h. The final products were analyzed with XRD. It was found that at 720°C, aluminum reacts with FeTiO3, forming Fe, TiO2 and Al2O3. Since the aluminum content used in the mixture was more than the stoichiometry for reaction of ilmenite and aluminum, some unreacted aluminum remains. Therefore, the residual aluminum reacts with the reduced Fe to form Fe2Al5.
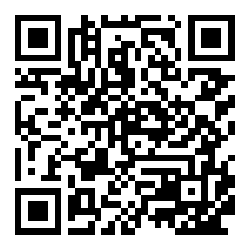
A. Kazazi, S. M. Montazeri, S. M. A. Boutorabi,
Volume 17, Issue 4 (12-2020)
Abstract
In the present study, austempering heat treatment was performed on compacted graphite aluminum cast iron with the chemical composition of 4.8%wt Al, 3.2%wt C, 0.81%wt Ni, 0.37%wt Mn, and 0.02%wt Mg. This study aims to investigate the effect of aluminum additions and removal of silicon on the kinetics of austempering transformation of Fe-3.2%C alloy. The cast samples were austenitized at 900 °C for 120 min and the isothermal austempering heat treatment was performed at 200 °C, 300 °C and 400 °C for 5, 30, 60, 120 and 180 minutes, respectively. Kinetics of this transformation was studied by X-Ray diffraction (XRD) analysis. The effect of temperature and time on the microstructure and hardness of the austempered samples was investigated and discussed. The presence of Al was seen to prolonged formation of the carbides from high carbon austenite, and that expanded the process window in the austempering transformation. Besides, the lower bainitic ferrite phase was observed in the austempered samples at 200 °C and 300 °C. Increasing austempering temperature to 400 °C changed the lower bainite to upper bainite structure. The volume fraction of austenite reached its maximum level (34.6 %) after austempering the samples at 400 °C for 30 minutes.
Saeid Karimi, Akbar Heidarpour, Samad Ghasemi,
Volume 18, Issue 2 (6-2021)
Abstract
In this research, expanded graphite (EG) was successfully fabricated using a simple ball milling process followed by hydrofluoric (HF, 10 wt. %) leaching. The effects of ball milling time (0-15 h) and leaching time (1-24 h) on the exfoliation of graphite were examined by XRD and Raman spectra. Furthermore, the morphological evaluation of the obtained expanded graphite samples was carried out by scanning electron microscopy (SEM). The XRD results of the ball-milled and HF treated samples showed a slight peak shift and broadening of (002) plane for expanded graphite compared to the precursor and HF-treated samples. Moreover, the intensity of the (002) planes remarkably decreased by the ball milling process but remained constant after HF treatment. Raman spectra of the samples confirmed the ordering process only in HF-treated specimens. Moreover, the intensity ratio of 2D1 to 2D2 band gradually increased with enhancing the HF treatment time up to 5 hours, indicating a decrement in the number of graphite layers by leaching in the HF solution.
Razieh Khoshhal, Seyed Vahid Alavi Nezhad Khalil Abad,
Volume 20, Issue 1 (3-2023)
Abstract
- In this article, the effect of graphite on iron-silicon interactions was investigated. It was found that, as graphite enters the iron structure, it permits further development of iron-silicon reactions. It was found that in the stoichiometric ratio of 1:0.5 of iron and silicon, when graphite is added to the system, simultaneously with the reaction of iron and silicon to form Fe3Si5, some amount of carbon can be dissolved in the iron and lead to more diffusion in iron and more iron silicide production. Silicon also reacts with carbon and produces SiC. The more amount of carbon entered into the system, the more growth of SiC occurs, while the production of other iron silicide phases, namely FeSi and Fe3Si preceded. Finally diffused carbon into the iron reaches a definite amount that can form Fe3C. In the stoichiometric ratio of 1:1 of iron and silicon, the formation of FeSi and SiC phases is observable. At the same time, the diffusion of carbon occurs in the same as the previous stoichiometric ratio. In the stoichiometric ratio of 1:2 of iron and silicon, compared with the stoichiometric ratio of 1:1, a larger amount of silicon is available and, the FeSi2 phase can form in addition to FeSi