R. Khoshhal, M. Soltanieh, M. A. Boutorabi,
Volume 13, Issue 1 (3-2016)
Al2O3/TiC composites are used as cutting tools for machining gray cast iron and steels. The addition of iron improves the toughness of Al2O3/TiC composites. Ilmenite, aluminum and graphite can be used to produce in-situ Al2O3/TiC–Fe composites. However, the formation mechanism and reaction sequences of this system are not clear enough. Therefore, the present research is designed to determine the reactions mechanism of the first step of reactions that may be occurred between raw materials. In this research, pure ilmenite was synthesized to eliminate the effects of impurities available in the natural ilmenite in the system. The milled and pressed samples, prepared from the synthesized ilmenite, aluminum and graphite mixture with a molar ratio of 1:2:1, were heat treated at 720°C for 48h. In addition, two samples one containing ilmenite and aluminum with a molar ratio of 1:2 and ilmenite and graphite with a molar ratio of 1:1 were heat treated at 720°C for 48h. The final products were analyzed with XRD. It was found that at 720°C, aluminum reacts with FeTiO3, forming Fe, TiO2 and Al2O3. Since the aluminum content used in the mixture was more than the stoichiometry for reaction of ilmenite and aluminum, some unreacted aluminum remains. Therefore, the residual aluminum reacts with the reduced Fe to form Fe2Al5.
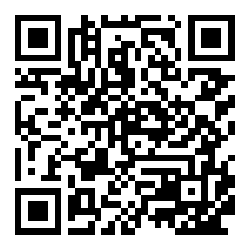